In the fiercely competitive world of the oil and gas sector, the corporations strive to be cost-effective while also remaining profitable and sustainable.
In the oil and gas industry, the Internet of things (IoT) refers to a network of physical objects with remote sensors, machine learning, and the cloud that are deployed in the upstream, midstream, and downstream operations for easy data collection, processing, and leveraging that data to streamline and simplify processes and supply-chain visibility, as well as drawing insights from that data for more quickly and accurately making decisions.
What Is IoT in the Oil and Gas Industry?
The global IoT market for oil and gas is projected to reach $43.48 billion by 2024, growing at a CAGR of 21.86% between 2019 and that year.
IoT adoption has revolutionized the oil and gas industry due to the inherent advantages of granting access to real-time information across remote sites, making operations efficient and safer for people.
The oil and gas industry’s rapid adoption of IoT has raised operational productivity by lowering manual labor.
It allows for real-time data monitoring of the machinery, as well as production optimization and growth.
The safety and security of resource extraction and distribution have dramatically improved as a result of IoT technologies that automate the processes, greatly lowering the possibility of human error.
This method also helps to boost production productivity by 6-8% by utilizing the data analytics that go along with it.
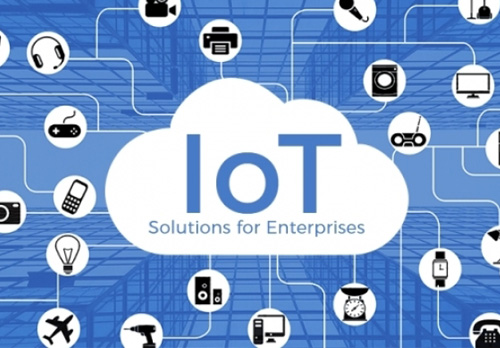
How IoT is transforming the Oil and Gas Industry
The oil and gas sector is making progress toward achieving the potential of IoT by making it considerably simpler for businesses to do their regular business. Here are some ways that IoT adoption in oil and gas operations is transforming the sector:
Drilling management
Drilling is frequently utilized in oil and gas operations. Increasing drilling efficiency turns out to be a benefit of the Internet of Things. The situation becomes riskier as the rig descends deeper. Rig workers must take exact measurements when drilling for oil. The inadequate technique is the cause of deep-water drilling errors.
IoT devices help lower risks and successfully perform challenging tasks. Smart gadgets can also alert worried employees well in advance of potential drilling issues using the data obtained by sensors.
Monitoring of pipelines
One of the biggest problems the oil and gas business has to deal with is pipeline leaking. The corporation suffers significant monetary, environmental, and reputational losses. IoT supports the pipeline system’s pipes, pumps, and filter monitoring. Without IoT, businesses are forced to rely on human resources to regularly do essential inspections and maintenance.
IoT can monitor pipelines in real time, reducing the need for manual checks. Real-time data can considerably reduce the most significant risks associated with pipeline leakages and other undesirable scenarios. Employees can be rapidly used to address problems that pose a severe threat.
Another benefit of IoT deployment in the oil and gas industry is the efficient management of personnel and the facility. Employees won’t be required to do maintenance until an anomaly is discovered.
As a result, routine human inspection is no longer necessary, and human resources may be managed successfully. IoT can also be used for efficient material management and planned shutdowns.
Refinery surveillance
IoT supports monitoring several performance indicators, including pipe pressure and flow rate. Every refinery component needs to be measured, and a lot of data is collected about it. If done manually, this takes a lot of time and costs the organization a lot of money. Real-time measurements are required in some situations.
For instance, a specific valve may need to be controlled based on the flow rate being monitored at another location. In this scenario, a change in flow rate would necessitate immediate control of the valve. The IoT enables more precise data collection at locations inaccessible to human resources.
More data can be obtained by installing sensors at various locations that are challenging for personnel to access. This facilitates the refinery’s constant observation. A report claims that effective data use can increase oil and gas businesses’ production by 6% to 8%.
Offshore monitoring
The majority of offshore oil and gas production occurs in challenging circumstances. There aren’t many communication networks accessible at these rigs. It becomes difficult and expensive to monitor equipment such as pressures, temperatures, and other variables.
IoT supports overcoming these obstacles to provide a trustworthy monitoring solution. With LPWAN, a huge number of monitoring points can be connected. This implementation offers a cost-effective solution for keeping tabs on offshore oil and gas rigs.
Oil wells can be linked to numerous leak detectors spread out across a large area. These detectors are capable of real-time data transmission to a central point. The data can then be utilized to remotely monitor the drilling and oil extraction process.
Cargo shipping
For fleet managers, real-time ship and fleet monitoring is a crucial component. Monitoring of cargo ships carrying oil and gas is comparable to offshore monitoring. The workers must use satellite internet because there is no connectivity at the ocean.
If the workers require information from the ship’s surroundings, their options are limited. The amount of data from these ships is enormous. IoT makes it simple to collect data from these points. LPWANs offer simple monitoring alternatives for areas of a ship that crew members don’t frequently visit.
Sensory monitoring tools offer simplicity and safety while collecting data from difficult-to-reach locations. Due to immediate needs, some cargo ship components must be wired, while some non-operational components are exempt from this need.
Health & safety
Oil and gas operations are typically found in hazardous and remote locations. For the personnel there, the surroundings at these places are hazardous.
IoT solutions provide remote monitoring of equipment and operations, doing away with the requirement for workers to physically visit a spot unprepared for the situation. With the help of networked sensors and picture vision, the situation may be precisely characterized, and the best course of action can be decided.
IoT has the potential to significantly reduce worker fatalities and injuries in the oil and gas sector. The oil and gas industry fatalities are declining, and IoT can help them stay that way.
Controlling Carbon footprint
Implementing IoT in oil and gas operations has improved the sector’s efficiency. IoT technology shows advantages in terms of money and the environment. The facility’s carbon emissions can be significantly reduced with efficient administration and operation.
It helps lessen the harmful effects of drilling and oil extraction on the environment. Thus, oil and gas companies can uphold their moral duty to conduct business in a way that doesn’t harm the environment.
Supply-chain management (SCM)
The oil and gas industry has long had difficulty planning and optimizing stockpiles. Effective planning and scheduling are made possible throughout the supply chain by IoT.
Refineries can utilize sensors to determine the sorts of crude oil that are delivered and the exact location where the barrels are stored.
These facts can be used to make decisions on operations and production. Thanks to the adoption of IoT, the oil and gas supply management chain will be more open and genuine.
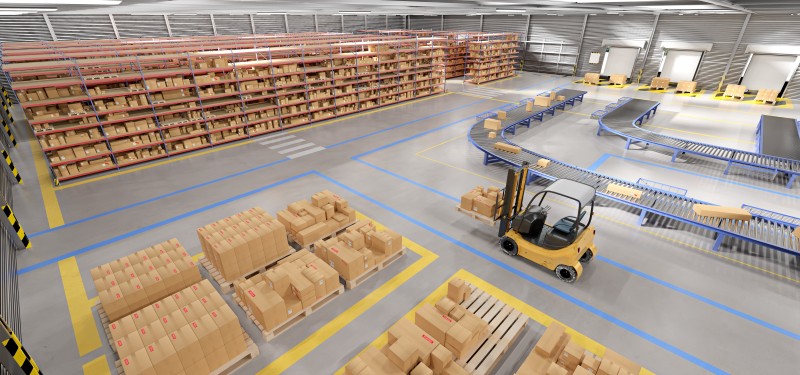
Growth in revenue
Recent years have seen an increase in rivalry for oil and gas companies. The best companies are looking for ways to raise productivity and sales. Short-term cost-cutting tactics may hinder a company’s long-term prosperity. If businesses invest in IoT, they will be more successful in reducing their operating costs.
IoT technologies could foresee demand and supply, boost productivity, and streamline pricey procedures. By minimizing wasteful capital and human resource consumption, businesses can significantly cut operational costs.
In Summary
Developing ‘smart’ oil and gas will continue to be a protracted, dynamic process. IoT solutions are moving from manufacturing facilities to boardrooms. Thus, the usage of IoT in the oil and gas industry extends beyond just the operations of the plant and rig and encompasses many, if not all, areas.
A new era of efficiency and profitability for participating organizations is being ushered in by the IoT and the data produced by these devices.